ball mill working principle and calculation
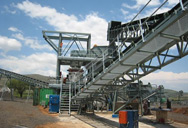
(PDF) Grinding in Ball Mills: Modeling and Process
2012.6.1 ... A ball mill is a type of grinder widely utilized in the process of mechanochemical catalytic degradation. It consists of one or
اObtener precio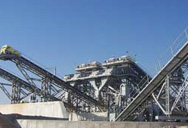
The working principle of ball mill - Meetyou Carbide
2019.5.22 The ball mill consists of a metal cylinder and a ball. The working principle is that when the cylinder is rotated, the grinding body (ball) and the object to be polished
اObtener precio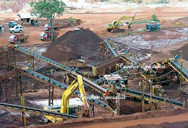
ATTRITORS AND BALL MILLS HOW THEY WORK Robert E
2021.2.4 The principle of Attritor dry grind processing is achieved by an expanded moving bed of media. This condition is described as kinematic porosity. The dry particles
اObtener precio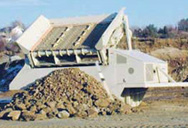
Ball Mill - an overview ScienceDirect Topics
It is possible to make an approximate calculation of the capacity of a ball mill by means of the equation: where ρ b.ap is the apparent density of the balls; l is the degree of filling of
اObtener precio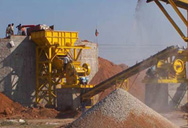
The working principle of ball mill - Meetyou Carbide - 美特优 ...
2023.6.25 材料周刊. 2019 . 5 . 22 . The ball mill consists of a metal cylinder and a ball. The working principle is that when the cylinder is rotated, the grinding body (ball)
اObtener precio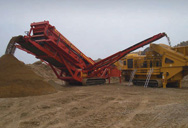
Ball Mill Design/Power Calculation - 911 Metallurgist
2015.6.19 Ball Mill Power Calculation Example #1 A wet grinding ball mill in closed circuit is to be fed 100 TPH of a material with a work index of 15 and a size distribution of 80% passing ¼ inch (6350 microns). The
اObtener precio
(PDF) Design of Three-chamber Ball Mill
2021.1.1 Its working principle is that the movement and force are transmitted to the barrel of ball mill through reducer, transmission shaft and hollow shaft by motor. Through the continuous...
اObtener precio
Ball Mill: Operating principles, components, Uses,
2022.11.30 Pharmaceutical uses of Ball Mill. 1. The small and average capacity ball mills are used for the final grinding of drugs or for grinding suspensions. 2. The maximum capacity ball mills are used for
اObtener precio
Closed circuit ball mill – Basics revisited - ScienceDirect
2013.4.1 Circulating load and classification efficiency effect on ball mill capacity revisited. Relative capacity model introduced and validated. Relationship between
اObtener precio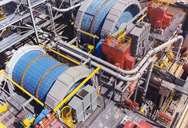
Calculation method and its application for energy consumption of ball ...
Owing to the lack of effective energy consumption models of ball mills in the ceramic industry, a calculation model to forecast energy consumption of ceramic ball mills during
اObtener precio
Stirred media mills in the mining industry: Material
2020.6.1 Use the mean G Pr of the last three cycles as the ball mill G Pr, and use this mean G Pr in the following calculation to determine the Bond Ball Mill Index Wi BM, in kWh/t: (14) Wi BM = 49.05 P 100 0.23 G pr 0.82 10 P 80 − 10 F 80 where P 100 is the closing screen aperture size (which separates net product from recycled coarse oversize material).
اObtener precio
(PDF) Operation Analysis of a SAG Mill under
2020.10.9 The mill speed, fill level ratio, and steel ball ratio can significantly affect mill operation, and our conclusions can provide a reference for an actual situation. Breakage parameters. Collision ...
اObtener precio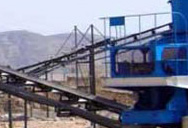
Ball milling as a synthesis method - Aalto University Wiki
2022.4.4 Introduction. Ball milling is generally known as a method to mix, blend, shape and reduce particle sizes. It can also be used as a mechanical synthesis method to produce materials that are milled to extremely fine powders. Several factors, like milling temperature, type of mill, milling speed etc. need to be considered when using ball milling ...
اObtener precio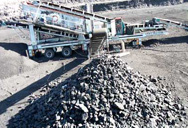
Closed circuit ball mill – Basics revisited - ScienceDirect
2013.4.1 Closed circuit milling flowsheet. The total solids mass flow of the mill discharge is: (2) Q + CQ = Q ( 1 + C) The final product mass flow in the mill discharge is Q / E and the amount of final product in the circulating load is: (3) Q E - Q = Q 1 E - 1. The mass flow of the coarse material in the mill discharge is the difference between the ...
اObtener precio
Rod Mill SpringerLink
2023.5.3 Download reference work entry PDF Rod mill is a roller-type grinding device with a long and round metal rod as the roller. In 1870, a rod mill with uniform discharging particle size was developed on the basis of the ball mill. ... the diameter of the overflow rod mill’s discharge port is larger than that of the overflow ball mill of the same ...
اObtener precio
Module-7 unit-3 NSNT Module 7 Ball-milling
2023.8.28 Alloys can be prepared by using different equipments such as, attritor, planetary mill or horizontal ball mill. The working principle for all these techniques is same. During alloy formation using ball-mill, two processes simultaneously occur: (a) fracturing, and (b) cold welding of powders. Thus, it becomes
اObtener precio
DE-11: Lesson 43. SIZE REDUCTION - e-Krishi Shiksha
This combination of impact and shearing forces brings about a very effective size reduction. Ball sizes are usually in the range 1 – 6 inches. Small balls give more point contacts but larger balls give greater impact. As with all grinding mills, working surfaces gradually wear, so product contamination must be guarded against.
اObtener precio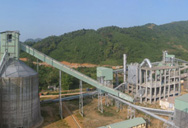
Tubular Rod Mills - ScienceDirect
2016.1.1 Grindability index for the ball mill = 12.0 kWh/t. Product size from the ball mill = 150 μm. Determine the size of the ball mill operated in closed circuit. Solution Step 1. The discharge from the rod mill is the feed to the ball mill. Therefore, in this case, the work, W, will be W = 12.0 × 10 1 150 − 1 1000 kWh / t. Step 2 Corrections to ...
اObtener precio
Ball Mills - 911 Metallurgist
2017.2.13 In all ore dressing and milling Operations, including flotation, cyanidation, gravity concentration, and amalgamation, the Working Principle is to crush and grind, often with rod mill or ball mill, the ore in order to liberate the minerals. In the chemical and process industries, grinding is an important step in preparing raw materials for subsequent
اObtener precio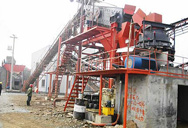
(PDF) Cements ground in the vertical roller mill
2013.3.1 C. Obry. Karl-Heinrich Zysk. Vertical roller mills are the mills traditionally used for processing granulated blastfurnace slag and for grinding composite cements. From the energy aspect they are ...
اObtener precio
Bead Mill, Principle and Applications / Apex Mill
1. General knowledge of bead mill. The bead mill is an apparatus that agitates grinding media (beads) in a cylindrical vessel to grind or disperse minute particles in slurry. The rotor of the mill generates bead motion,
اObtener precio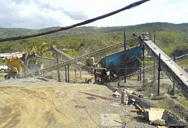
Comparative study of SPEX and planetary milling methods
2018.4.1 The objective of the present work is the comparison of two common milling methods for the production of complex metallic alloy nanoparticles. γ-Al 12 Mg 17 nanoparticles were fabricated using both a planetary ball mill and a SPEX mill. The produced nanoparticles have been compared on the basis of the phase and microstructural
اObtener precio
Ball Mill- Principle, Application, Uses, Critical Speed, Diagram ...
2023.2.25 Ball Mill- Principle, Application, Uses, Critical Speed, Diagram Important Info 2023 ... Understanding the various parts of a ball mill and how they work together is essential for efficient operation and maintenance. ... Important Dilling’s Rule Dose Calculator 2023 22/08/2022. Size Reduction MCQ with answers 08/10/2021.
اObtener precio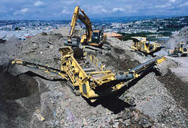
Energy-Efficient Technologies in Cement Grinding IntechOpen
2016.10.5 The energy consumption of the total grinding plant can be reduced by 20–30 % for cement clinker and 30–40 % for other raw materials. The overall grinding circuit efficiency and stability are improved. The maintenance cost of the ball mill is reduced as the lifetime of grinding media and partition grates is extended. 2.5.
اObtener precio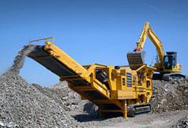
Roller Mill Based on Experimental Method - mdpi-res
2022.1.23 mill, coal mill, Clinker Mill and cement mill, and the vertical mill occupies a large energy consumption unit. Therefore, it is necessary to optimize the multi-objective parameters of the VRM in order to improve the grinding performance and reduce energy consumption. The present work focuses on the grinding performance of an overflow ...
اObtener precio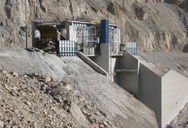
Operational parameters affecting the vertical roller mill
2017.4.1 Grinding test results for zinc ore showed that it is possible to decrease the total grinding energy consumption from 20.11 to 11.40 kW h/t by using vertical roller mill instead of AG/SAG-ball mill circuit (van Drunick et al., 2010). In another test performed in the Loesche test centre in Germany, 22.9% in airflow-mode and 34.4% energy savings ...
اObtener precio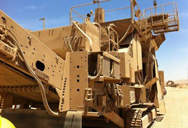
An innovative approach for determining the grinding
2021.1.22 When the internal diameter of the ball mill was over 3.3 m, S S was calculated through equality (16) [32]. B was the maximum diameter (50 mm), and D the effective inner diameter of the ball mill (4.916 mm). (16) S S = 1.102 × B − 12.5 D 50.8 (4) The calculation of motor power of ball mill. The media addition was calculated via
اObtener precio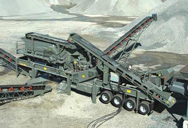
Critical rotation speed for ball-milling - ScienceDirect
1999.8.3 2. Experiment. To examine the dependence of critical rotation speed on ball-containing fraction, we measured critical speeds at various ball-containing fractions from 0.3 to 0.95 stepped by 0.05. Since at lower fraction than 0.3 we could not observe the centrifugal motion, we chose this fraction range. A jar of ball-mill consists of a cylinder ...
اObtener precioMas noticias
- estator molino sag de minera collahuasi
- mabati laminadores productos precios
- fabricante de planta de refinería de oro
- trituradoras de carbón de equipos
- molino de bolas usados para la venta toneladas por houre
- moderno proceso de molienda de cemento
- planta de trituracion de piedra caliza
- molino para motosierras
- trituradora de mineral de hierro ahorra nagpur
- dise ntilde o del molino de bolas para vidrio
- mineral de hierro separador magnetico seco
- Liming trituradora de impacto PF horizontal
- precisión móvil purificador de aceite y el aceite de la planta de llenado
- operaciones de molienda ppt
- molino martillo arena
- partículas ciclón grind separación
- NUEVA MAQUINA PARA HACER HELADOS YouTube
- Centro Eventos Molino
- en ayutla promulgado
- molino electrico mercadolibre
- diagrama de flujo de trituradora de agregados
- precio de la trituradora de cono t h cg
- aceite comestible maquinaria del molino
- fabricante de trituradora de piedra de mampostería en la mexico
- trituradora de quijada de 2 o 3 toneladas
- trituradoras de cono en venta aus
- lavadoras rommer repuestos
- chancadora de piedra camión
- como construir una cinta transportadora para mosaicos
- planta de la máquina de polvo de mármol